
In today’s manufacturing industry, your reliance on technology is more critical than ever. The seamless integration of IT support in your manufacturing operations can lead to increased productivity and efficiency (which is even more true in the case of financial services companies).
With the fast pace of innovation, keeping your production lines running smoothly without hiccups requires a robust IT infrastructure. The support provided by IT teams ensures that the advanced machinery and software you employ are always operating at peak performance, minimising downtime and maximising output.
As you navigate through the complexities of modern manufacturing, technology becomes your backbone. IT support plays a vital role in troubleshooting issues, implementing new systems, and maintaining the cybersecurity of your operations. It helps you adapt to changes quickly, be it in responding to market shifts or adopting new technological advancements. This adaptability, underpinned by solid IT support, is what enables you to stay competitive and meet the ever-increasing demands of your customers.
Moreover, IT support is not just about fixing problems when they arise; it’s also about anticipating potential challenges and preparing for them. By having dedicated IT professionals on your team, you can ensure that the latest updates are rolled out smoothly, security protocols are up to date, and your data is backed up. Understanding the intricate relationship between your manufacturing processes and technology is vital for your business’s success, and it is here that IT support bridges the gap, driving innovation in every corner of your industry.
The Evolution of Technology in Manufacturing
The manufacturing sector has experienced a significant shift with the incorporation of advanced technologies. You’ve likely heard terms like Industry 4.0 and digital transformation, but what do they actually mean for the industry?
From Industry 3.0 to 4.0
Industry 3.0 marked the introduction of computers and automation into manufacturing. But Industry 4.0 takes it a leap further by blending physical production with smart digital technologies. Artificial Intelligence (AI), cyber-physical systems, and cloud computing are at the heart of this transformation. They have enabled machines to communicate and make decisions, pushing the boundaries of what’s possible in manufacturing.
AI has become your ally on the factory floor, predicting maintenance and optimising processes. Cyber-physical systems, which integrate physical operations with computer-based algorithms, now adjust to changes in real-time and improve efficiencies. For you, this means products can be made faster, safer, and to a higher quality.
Impact of IT on Production Systems
Your understanding of digital transformation shapes how well you can leverage it for production systems. By introducing IT, traditional production lines have become more flexible, adaptive, and responsive to market demands.
Technology | Benefits for Production Systems |
Big Data Analytics | Enhanced decision-making and predictive maintenance |
Additive Manufacturing | Customisation and reduced waste |
Robotics | Increased productivity and human-robot collaboration |
Data analytics has empowered you to predict machine failures before they happen, improving productivity and reducing downtime. Additive manufacturing, also known as 3D printing, has given you the ability to create complex parts on-demand, opening up new avenues for customisation. You’ve seen robots become more collaborative, working alongside humans to complement their skills.
In essence, IT in manufacturing equips you with the tools to not only survive but to thrive in a competitive market by embracing the digital age.
IT Infrastructure in Manufacturing
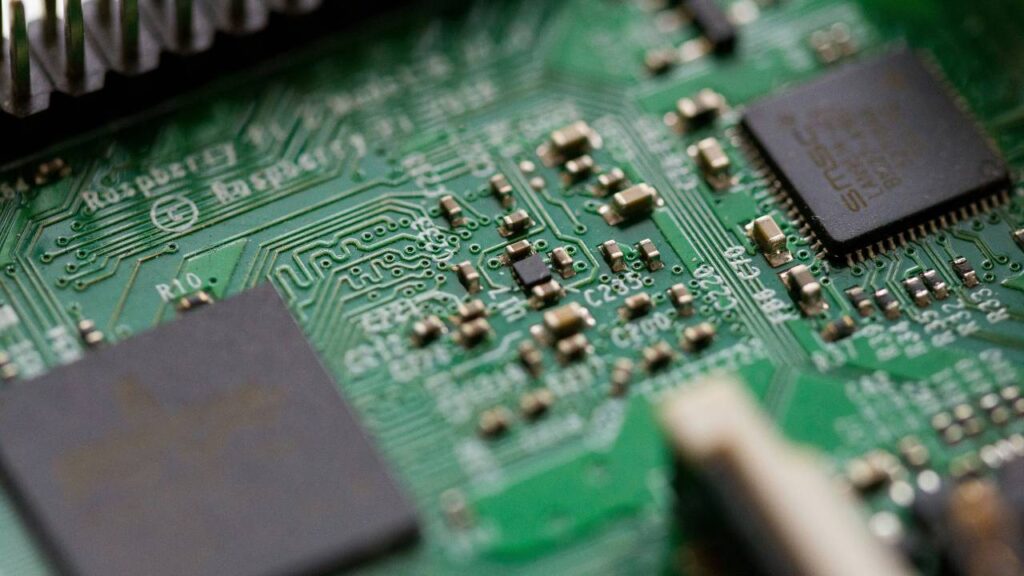
In manufacturing, an efficient IT infrastructure underpins the entire operation, facilitating better data management and secure information flow. Your modern factory relies heavily on the robustness of these systems.
Network Infrastructure and Data Management
Your network infrastructure is the backbone of your manufacturing processes. It supports the vast array of connected devices and machinery that are pivotal to your operational efficiency. With proper network management, you’ll experience seamless data flow across the system, enabling real-time data analysis that can drastically optimise production processes.
- Components – Routers, switches, wireless access points.
- Benefits:
- Enhanced communication among devices.
- Improved data throughput, avoiding bottlenecks.
IT Systems and Manufacturing IT Services
IT systems and services in manufacturing are tailored to support industry-specific workflows. They ensure the seamless transition from raw materials to finished goods through meticulous tracking and management of resources. An integrated IT service within your manufacturing setup can lead to better inventory management, streamlined production scheduling, and even predictive maintenance planning thanks to advanced data analysis.
- Key IT Systems:
- Enterprise Resource Planning (ERP).
- Manufacturing Execution Systems (MES).
- Supply Chain Management (SCM).
Cybersecurity Measures
Your manufacturing IT infrastructure must be fortified against cyber threats, including data breaches that can have dire consequences. Cybersecurity measures should be integrated deeply into your IT systems, not only to protect sensitive information but also to safeguard the continuity of your manufacturing operations. Employing a multi-layered security approach combines the use of firewalls, intrusion detection systems, and regular security audits to mitigate risks.
- Practices to Enhance Security:
- Regular software updates to patch vulnerabilities.
- Employee training to recognise phishing attempts.
Optimising Efficiency and Productivity
Enhancing your manufacturing operations requires a strategic approach to integrating IT support. By focusing on automation and implementing rigorous IT for quality control, you can significantly boost both efficiency and productivity.
Automation and Robotics
Your adoption of automation and robotics has a profound impact on manufacturing efficiency. Automated systems are designed to handle repetitive tasks more quickly and with greater precision than human workers. For example:
- Robots carry out tasks such as welding and assembly, reducing the scope for human error.
- Machine learning algorithms optimise production schedules and maintenance tasks, minimising downtime.
By leveraging these advancements, you can not only speed up production but also allocate your workforce to more complex tasks, enhancing overall productivity.
Implementing IT for Quality Control
Ensuring the high quality of your products is a key part of maintaining productivity. Implementing IT for quality control brings numerous benefits, such as:
- Real-time Monitoring – IT systems enable continuous monitoring of production processes, facilitating the early detection of anomalies or defects.
- Data Collection – Sensors and cameras collect data that are analysed for quality assurance.
- Predictive Maintenance – Machine learning algorithms predict equipment failures before they occur, allowing for preventative maintenance and reducing costly downtime.
By strategically applying IT support in these areas, you can simultaneously preserve the quality of your products while streamlining your operations to minimise waste and maximise output.
Strategic Decision-Making with IT
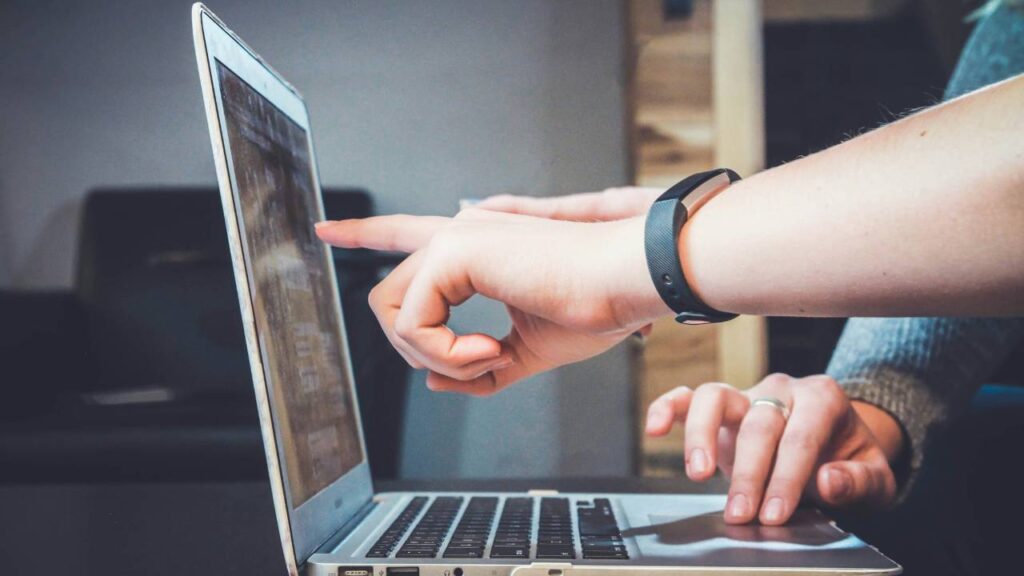
Information Technology (IT) plays a pivotal role in enhancing your manufacturing operation’s strategic decisions. Utilising Data Analytics and predictive tools helps you make informed decisions that streamline operations and promote efficiency.
Data Analytics and Business Intelligence
Your grasp of Data Analytics is crucial for extracting valuable insights from the immense volume of data your manufacturing business generates. Tools in Business Intelligence (BI) arm you with the power to monitor and manage production performance meticulously. For instance, you might use analytics to track and improve supply chain efficiencies, or to reduce waste by identifying bottlenecks in production processes. Effective data management means you have access to real-time data and can swiftly adapt to changes in the market or production.
- Key uses of Data Analytics in manufacturing:
- Real-time monitoring – Tracking production lines for immediate response to issues.
- Quality control – Analysing production data to maintain high standards.
Predictive Analytics and ERP Systems
Predictive Analytics, when integrated with Enterprise Resource Planning (ERP) systems, empower you to foresee problems before they occur. By anticipating machine maintenance needs, you can schedule repairs during downtime, thus avoiding costly disruptions. Moreover, ERP systems coordinate all aspects of your operations, from inventory management to financial planning, ensuring that you can act not just reactively, but proactively too.
- Benefits of Predictive Analytics:
- Maintenance Scheduling – Preemptively arrange for equipment maintenance.
- Demand Forecasting – Predict market trends to effectively manage inventory.
With a robust IT support structure, your strategic decision-making is significantly more agile and informed, positioning you to outperform competitors and meet market demands with precision.
Achieving a Competitive Advantage
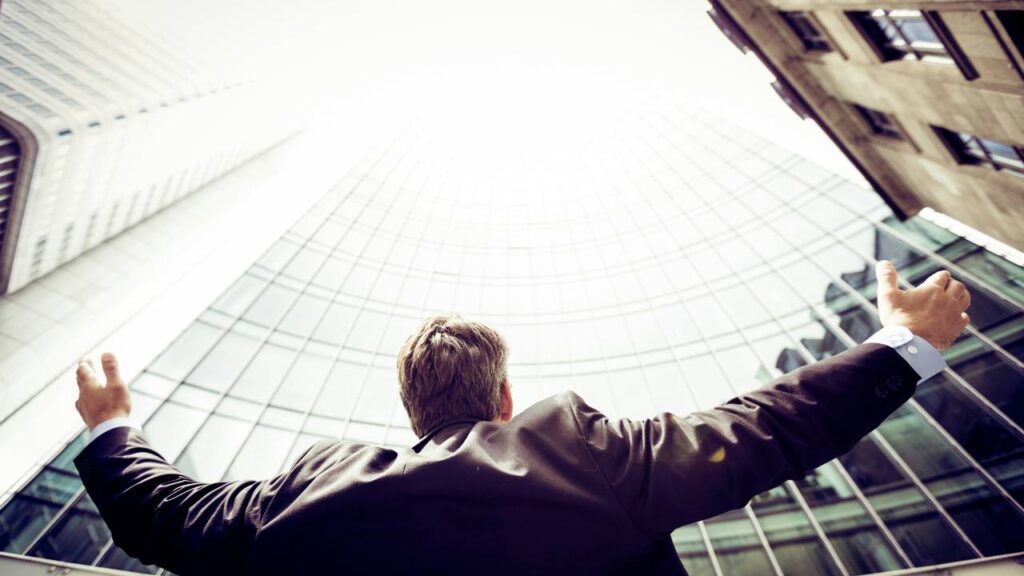
In today’s market, your ability to gain a competitive edge in manufacturing hinges on excelling in customer experience and adhering to stringent compliance standards.
Customer Experience and Market Competitiveness
To be competitive, you must prioritise your customers’ experience. This involves outsourcing IT support to ensure product quality and prompt delivery. Real-time data analysis can pinpoint process bottlenecks, allowing for quick resolution and maintaining product flow. Moreover, personalisation of products, enabled by advanced IT systems, caters to specific customer preferences, setting your services apart from competitors.
- Quality Assurance – Your use of IT in quality control automates defect detection, reducing return rates and increasing customer satisfaction.
- Delivery Optimisation – Advanced scheduling systems improve the efficiency of your supply chain, ensuring timely deliveries that bolster your market reputation.
Regulatory Compliance and Standards
Adherence to regulatory compliance and standards is not only mandatory, but it also serves as a significant aspect of your competitive advantage. IT support plays a crucial role in maintaining records, monitoring processes, and reporting in line with regulatory requirements.
- Record-Keeping – IT systems reliably track quality checks, inventory, and safety audits, ensuring that your business meets industry standards.
- Process Monitoring – Sophisticated software allows you to continuously oversee production, minimising risks of non-compliance.
By integrating stringent compliance measures and enhancing customer experiences through IT support, you solidify your competitive position in the manufacturing industry.